How AI Solves Top Challenges in Battery Manufacturing
How AI Solves Top Challenges in Battery Manufacturing
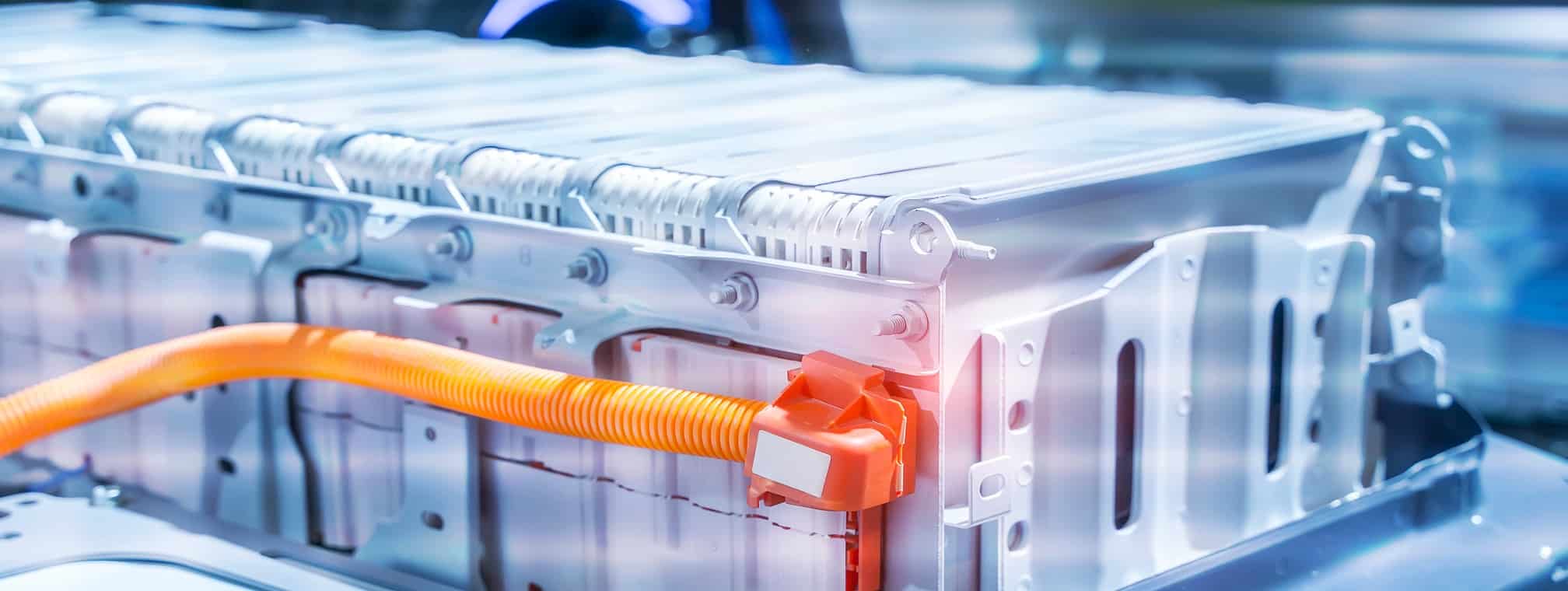
The surging global demand for batteries, driven by the electric vehicle (EV) and renewable energy revolutions, has put immense pressure on manufacturers to scale up production. At the same time, the fierce competition means unprecedented pressure to reduce costs. But scaling up battery manufacturing is not easy – it involves complex processes, new technologies, and tight quality requirements.
We at Elisa IndustrIQ, as leading experts in industrial manufacturing software, believe the solution lies in artificial intelligence (AI). Our modular software approach leverages data and machine learning to enable battery manufacturers to ramp up production quickly and cost-effectively, while ensuring high quality output. Here’s how.
The Ramp-Up Challenge
Battery manufacturing involves hundreds of process steps and parameters, with complex interdependencies. Ramping up production means fine-tuning all these elements concurrently, often with new technologies. This leads to unexpected process deviations that can cause yield losses and delays if not resolved quickly.
Traditional problem-solving relies heavily on time-consuming testing and experts analysing data manually. In a ramp-up scenario, where speed is critical and experts are scarce, this approach falls short. This is where Elisa IndustrIQ’s pioneering AI and ML enhanced manufacturing solutions come into play.

AI to the Rescue
Advanced algorithms can rapidly detect process anomalies by analysing the vast amount of data generated across the production line. More importantly, they can trace problems to their root cause and quantify the impact, enabling quick corrective action.
Let’s consider a specific example – the formation stage where the cell’s initial capacity is set. Defects originating upstream, like in electrode coating or electrolyte filling, often show up here. ML algorithms can classify cells as good or bad with 95%+ accuracy within the first few cycles, compared to weeks of testing needed traditionally.
The algorithms then scan through the entire manufacturing history – materials, design parameters, process settings, sensor data – to pinpoint the likely source of the problem. The results are served up to operators as actionable insights via our intuitive user interfaces, for example highlighting the specific equipment most strongly associated with bad cells. Armed with this, engineers can target fixes for maximum impact.

Towards Predictive Quality
As the system builds up historical data through successive rounds of root cause analysis, its power grows. The same algorithms can now predict quality in advance, allowing adjustments to be made proactively.
Imagine being able to ask: “For this batch of cells, with material properties A, design parameters B, and upstream process history C, what are the odds of getting good cells if I use downstream settings D vs E?” Operators can essentially simulate different scenarios to optimise production.
This predictive quality capability, powered by Elisa IndustrIQ’s AI solutions, transforms the ramp-up process from reactive firefighting to proactive continuous improvement. Each problem solved adds to the knowledge base, creating a virtuous cycle of higher yields and throughput.
The Digital Foundation
Implementing AI does require some groundwork. Comprehensive data collection and integration is a must, spanning material properties, design parameters, process settings and sensor readings. Often, this data exists in silos and needs to be consolidated and synchronised.
With battery manufacturing involving 2000+ parameters, data quality is key. While ML models can handle sparse data initially, accuracy improves as data volume and quality builds up. Connecting all equipment to a central data platform, such as Elisa IndustrIQ’s Manufacturing Operations Management (MOM) solution, is an essential first step.
Our powerful MOM solution flexibly combines essential modules that reflect best practices for increasing efficiency, quality, and reliability in battery manufacturing. It provides the necessary digital backbone to enable AI applications.
The Human-Machine Partnership
It is important to recognise that AI’s role is to augment human expertise, not replace it. The goal is to arm engineers with insights that sharpen their intuition and accelerate problem-solving. A plant may have numerous veteran operators with deep know-how; AI helps scale this expertise by making it accessible to all.
In our experience, a collaborative approach works best. We work closely with customers to identify high-impact use cases, evaluate data readiness, and integrate the AI platform with existing systems. From there, it’s a continuous partnership as the system learns and improves.
Elisa IndustrIQ’s customer-centric approach and decades of manufacturing expertise allow us to act as trusted advisors in this digital transformation journey. We emphasise the human element, ensuring that our AI solutions empower operators and engineers rather than overwhelm them.
The Battery Industry’s AI-Powered Future
As the battery industry hurtles forward, manufacturers that can scale up fastest will gain a decisive competitive edge. AI is emerging as a key differentiator, enabling order-of-magnitude improvements in production ramp-up speed and yield.
Beyond accelerating today’s production, AI is also key to tomorrow’s battery breakthroughs. The same techniques can speed up development cycles for new chemistries and cell designs. The deluge of data generated is a gold mine for innovation when harnessed with AI.
At Elisa IndustrIQ, we’re excited to be at the forefront of this digital transformation in battery manufacturing. Our mission is to help manufacturers leverage their data to solve complex challenges and accelerate their journey to AI maturity.
With our modular, industry-proven solutions tailored for the unique needs of battery production, we aim to be the partner of choice for forward-thinking manufacturers. From supply chain visibility to quality management to environment, health and safety compliance, our comprehensive software suite covers all aspects of the battery manufacturing lifecycle.
The era of smart, resilient, and hyper-efficient battery production is here – and it’s powered by AI. As your trusted advisors, we at Elisa IndustrIQ are committed to working alongside you, harnessing the power of cutting-edge AI solutions to achieve our shared goals. Let’s innovate together and shape the future of sustainable battery manufacturing.
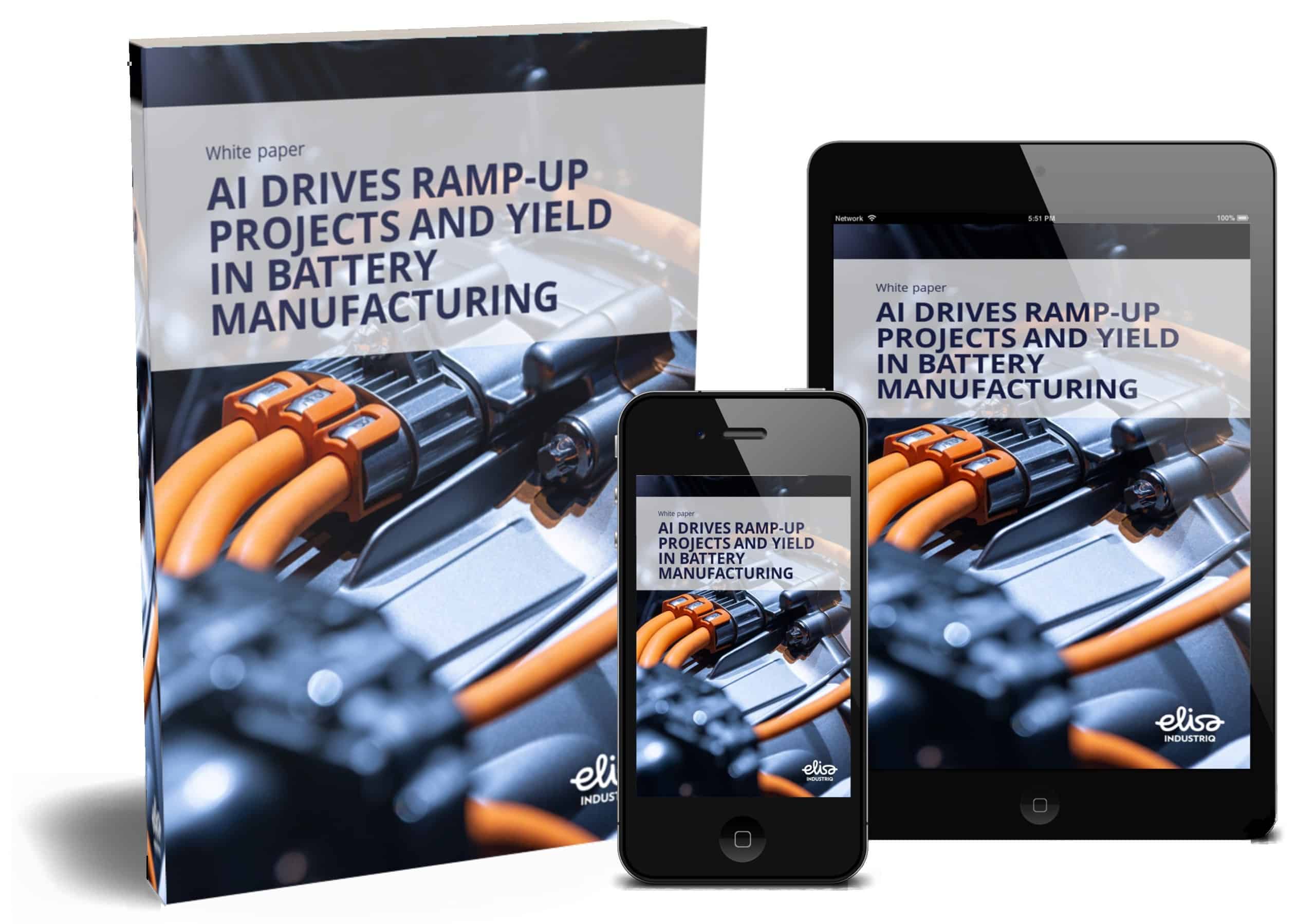
Read More in Our New White Paper
Learn more about how artificial intelligence (AI) can play a strategic role in battery manufacturing in this white paper. Senior Data Scientist Kalle Ylä-Jarkko explores the integration of machine learning in the dynamic market of battery manufacturing. Discover how AI can boost yield in battery production, the power of AI-driven automated root-cause analysis, predictive quaity, and more.